by Michael Lee, Vice President of Sales & Marketing, dB Control
There will always be emerging threats in the defense sector that require the innovation that millimeter-wave technology offers. Here’s a helpful Q&A primer on millimeter-wave products – including what specialized contract manufacturing and environmental testing can bring to the table.
Which defense applications need millimeter-wave frequency products?
Radar, electronic warfare and countermeasures, airborne datalink, and satellite communications markets are especially in need of millimeter-wave products. Why? Because next-gen tactical networks and electronic warfare are transitioning to higher frequency spectrums to defend against newly discovered threats. And with innovations like 5G, 6G and Satcom backhaul on the rise, connectivity, bandwidth and speed are hugely important in the commercial and defense sector.
What are the advantages/challenges of millimeter-wave technology?
Some advantages of millimeter-wave technology include much higher bandwidth, increased connectivity with many more channels, and faster exchange of data during tactical communication. Some challenges of millimeter-wave technology include an escalation in costs and complexity, as well as operational environmental challenges. Fortunately, the advantages outweigh the disadvantages.
What is the migration from traditional frequencies to higher frequencies?
Traditionally, products with C-, X- and Ku-band frequencies were used in many applications. But as military operations became more sophisticated and congestion increased in those bands, defense contractors and original equipment manufacturers began to see a thirst for more bandwidth. (See Figure 1.) That’s why electronic warfare, satcom and datalink applications are moving to millimeter-wave frequencies. As K-, Q- and V-band technology matures, original equipment manufacturers are modifying designs to produce products that meet the needs of modern military and commercial applications.

Figure 1: Migration of frequency band power capabilities
What frequency ranges are defense contractors seeking and why?
Defense contractors are seeking frequency ranges from 18 to 50 GHz. The specific frequency depends on the application. For electronic warfare (EW) applications, wideband and continuous wave (CW) power are required. For datalink and satcom applications, narrow band and CW power are required. For radar applications, narrowband and pulsed power are required.
dB Control offers four Microwave Power Modules (MPMs) and three Travelling Wave Tube Amplifiers (TWTAs ) developed specifically for millimeter-wave applications. The dB-3201 MPM, dB-3709i TWTA and dB-3861 TWTA are shown in Figures 2-4. Also available from dB Control are the dB-3202 MPM (27.5-31 GHz, 200W), dB-3201H MPM (30-38 GHz, 125W), dB-3860 TWTA (34.5-35.5 GHz, 700W), and dB-3205 MPM (34.5-45 GHz, 80W). Click here for more information on all of dB Control’s reliable, ready-to-ship power products for millimeter-wave applications.
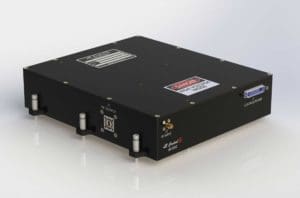
Figure 2: dB-3201 Microwave Power Module (26.5-40 GHz, 125W pulsed/CW RF output power) for ECM, electronic warfare simulation
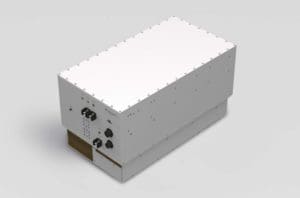
Figure 3: Hubmount dB-3709i KA Band TWT Amplifier (34.5-35.5 GHz, 700W pulsed) for radars, test and measurement, antenna pattern and radar cross-section measurements, EW simulation
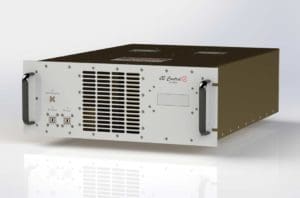
Figure 4: Rackmount dB-3861 TWT Amplifier, 32-38 GHz, 400W min. peak output, for radars, test and measurement, antenna pattern and radar cross-section measurements, EW simulation
What kind of environments will millimeter-wave products need to endure?
Any high-power TWTA or MPM should be equipped to withstand extremely complex conditions, and that complexity should be outlined from the very beginning. (See Figure 5.) For example, all millimeter-wave high-power amplifiers (HPAs) will need to endure very harsh environments with extreme temperatures, excessive vibration, shock, and altitudes up to 70 thousand feet above sea level. The HPAs must be tested to extreme levels to ensure they stay reliable even on the most rugged missions – including potential nuclear events.
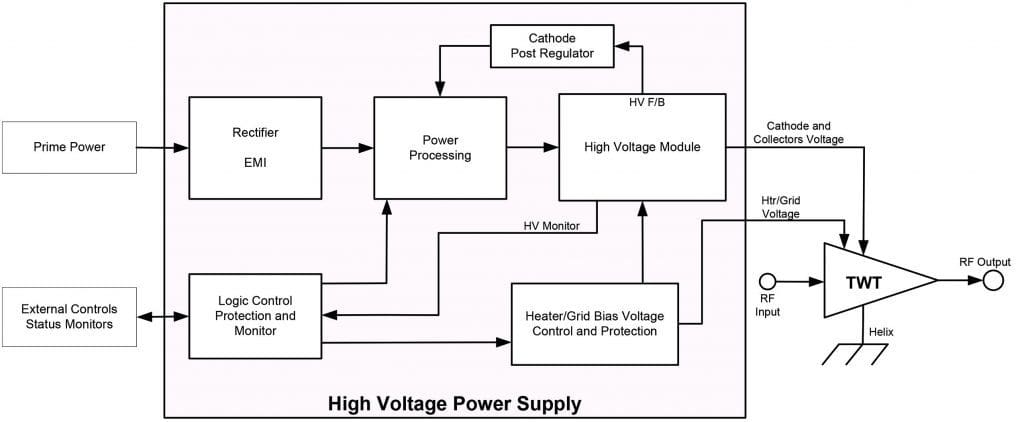
Figure 5: Block diagram of a high-voltage TWTA
What should the testing process look like for millimeter-wave HPAs?
Once a product design is established and preproduction runs are complete, full environmental testing and stress screening is required. The extensiveness of the testing minimizes replacement costs and downtime out in the field, as well as field infant mortality. Ideally, the manufacturer would have an onsite HALT/HASS machine to reduce processing time and labor costs. Millimeter-wave products also need to be tested in an automated 24-hour test cycle to ensure reliability and simulate a very long mission life in rugged settings. Environmental chambers should be programmed for custom combinations of temperature and altitude to match a mission’s profile. Additionally, vibration tables should be programed for the vibration and shock levels seen on the specific mission profile.
What makes an engineering and assembly team excel at producing millimeter-wave products?
Reliability must be incorporated from the very beginning – during the initial design phase. When you think about the end products, lives are on the line, so a manufacturer must master repeatability and reliability. Defense contractors should look for a manufacturer with a team of experienced, dedicated design engineers, test engineers and technicians. Professionals on the supplier’s manufacturing team should be specifically trained to work with high-voltage electronics and have extensive experience with millimeter-wave components. In addition, the manufacturer should have a proven track record of producing high-power amplifiers for airborne, maritime and ground-mobile deployments.
About the Author
Michael Lee is the Vice President of Sales and Marketing at dB Control. He has more than 25 years of RF and microwave experience developing relationships with companies whose specifications require high-power TWTAs, MPMs, power supplies, contract manufacturing services and repair depot services. Prior to joining dB Control, Lee worked at Comtech, Xicom Technology and IBM, where he received a U.S. Patent for his electrical circuit design. Lee holds a Bachelor’s of Engineering in Electrical Engineering from The City College of New York.
About dB Control
Established in 1990, dB Control Corp. supplies mission-critical, often sole-source, products worldwide to military organizations, as well as to major defense contractors and commercial manufacturers. dB Control is a subsidiary of the Electronic Technologies Group of HEICO Corp., a publicly traded aerospace and electronics company with more than 60 subsidiaries. dB Control designs and manufactures reliable high-power TWT amplifiers (TWTAs), microwave power modules (MPMs), transmitters, high- and low-voltage power supplies, and modulators for radar, electronic countermeasures (ECM), and data link applications. The modularity of dB Control’s designs enables rapid configuration of custom products for a variety of platforms, including ground-based and high-altitude military manned and unmanned aircraft. Acquisitions in 2019 (TTT-Cubed, Inc.),2021 (Paciwave, Inc.) and 2022 (Charter Engineering, Inc.) added custom RF sources and receivers, RF/microwave components and integrated subsystems, and precision electromechanical switches and components to the company’s product offerings. dB Control also offers specialized contract manufacturing and repair depot services from its modern 40,000-square-foot facilities in Fremont, California, and is AS9100D- and ISO 9001:2015-certified.
Download specs for our most highly requested millimeter-wave HPAs
Learn more about dB Control.
Email MLee@dBControl.com for more info
This article was published in the April 25, 2023 edition of the RF Globalnet Newsletter